Sheet materials play a pivotal role across manufacturing, construction and even the automotive sector. Available in a wide range of materials, from various wood types to plastic, metal, and glass; handling such material can pose significant challenges and even lead to workplace injury. Understanding and mitigating the present risks is fundamental to business operations and meeting Government health and safety regulations.
The Challenges of Sheet Material Handling
Sheet handling features numerous challenges for employees and business operations, affecting overall safety and processes.
Time Constraints
Sheet size can be cumbersome for individuals due to their bulky and difficult configuration. Multiple employees are often required to lift one sheet at a time, which slows down production time and creates potential safety issues.
Weight
The weight of sheet materials varies based on their intended application and sector. Sheet metal can easily reach 350kgs in weight, which requires correct lifting practices from multiple individuals at once. This is a non-efficient use of labour and effectively becomes a health and safety risk.
Limitations
Requiring employees to manually move sheet panels by hand ultimately limits the employer in hiring individuals who can physically do so. The integration of material handling equipment opens up the prospect for more hires that are of varying builds and capabilities, establishing an inclusive workplace.
Injury
Repetitive handling of long and heavy sheets over a long period of time can eventually lead to workplace injuries, such as musculoskeletal disorders, strains, sprains and back issues. All of these are detrimental to business operations, contributing to loss of earnings and productivity due to sick leave.
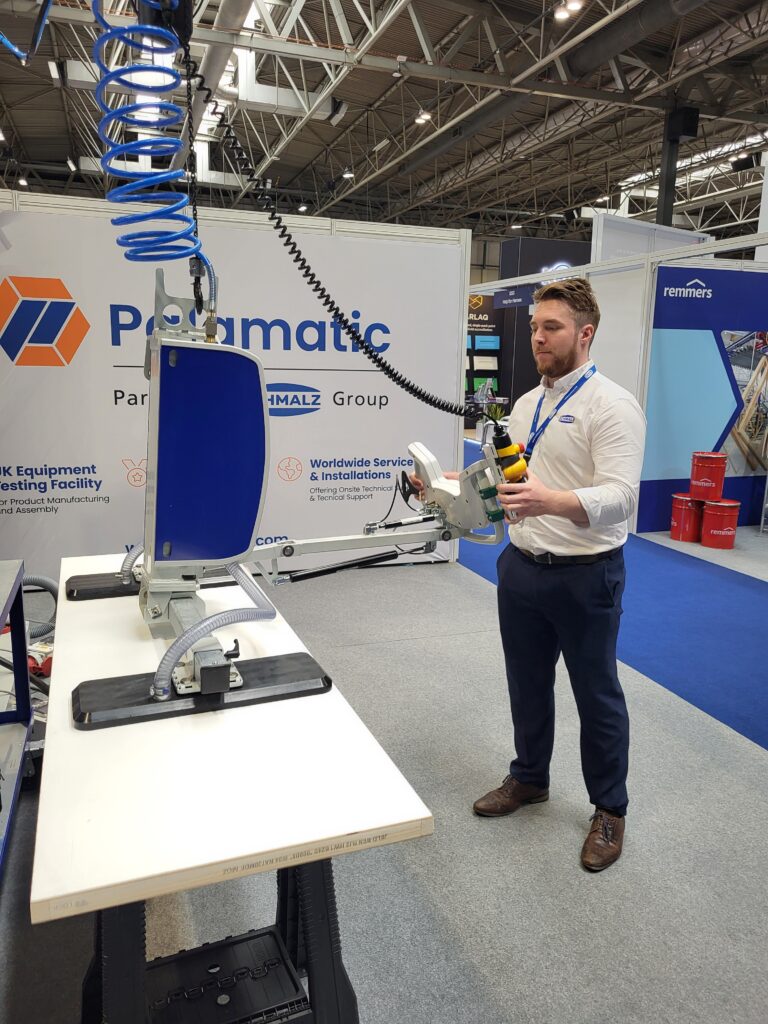
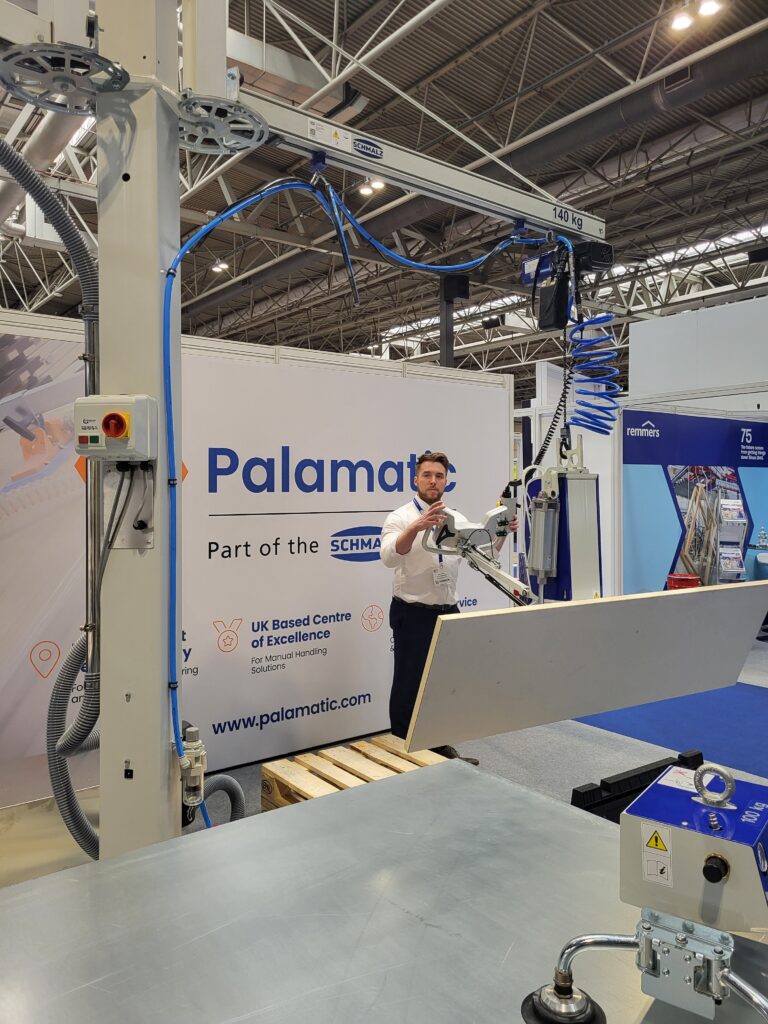
Material Lifting Solutions for Sheet Handling
Dedicated material lifting equipment, such as vacuum lifters, can make a significant difference in business operations and performance.
Vacuum Lifting Equipment
Vacuum lifting equipment utilises an electrical vacuum pump to create lift of heavy and difficult sheets, weighing up to 350kg. This is possible by a vacuum seal forming against the sheet upon contact with the suction pad. This creates intuitive material handling for the operator, with 90°, 180° and up to 360° rotation for certain materials-vacuum handling is proven as a robust and effortless approach for material lifting.
Automation
Part of a company’s processes is understanding how to streamline production, reduce waste and enhance downstream efficiency. Employees who are manually lifting materials can be reduced to just one operator, processing panels safer, faster and much more effectively. This establishes automation as part of regular business operations and opens opportunities for other areas of focus.
Quality
Various sheets can be difficult to handle, often in awkward configurations that can lead to bending and warping as handlers attempt to grab across the width span. This is especially prominent if there are not enough people to help carry the material, which can often be the case. Vacuum lifters utilise multiple feet which generates a powerful suction on the sheet, regardless of material type. This ensures the product is not at risk of falling mid-air, which is a key area of concern, especially with glass panels.
Eliminate Injury
Vacuum lifting equipment eliminates workplace injury by reducing the need for heavy lifting that can severely impact joints, muscles and tendons. In the UK alone, there were approximately 604,000 workplace injuries within the last year, according to the Labour Force Survey, with the majority occurring from falls and incorrect lifting.
Cost-Effective
The investment into vacuum lifting equipment in the long run is a cost-effective solution for the workplace. With regular maintenance from after-sale services and sufficient staff training, material lifting equipment lasts for several years.

Mitigating Injury in Sheet Handling
The average weight of a steel sheet is roughly 230kg, with the maximum safe lifting weight for an average man at 25kg, and 16kg for women. This results in requiring more individuals on hand, which is not always practical, or an increased risk of injury to an employee.
Injury can occur from repetitive motions over long periods, leading to back injuries, sprains, strains, musculoskeletal disorders and even broken bones in extreme situations. Although employers have a legal obligation to implement correct safety procedures and enforce ergonomic lifting techniques, this can often take a backseat by staff as routine and habits set in. The introduction of vacuum lifting equipment provides efficient measures against hazards and injury in several ways. However, operating a vacuum lifting machine correctly is still critically important to understand.
- Pre-Use Checks: Monitor the area before operation to avoid any hazards or adverse conditions. The equipment should be in good working order before use, with no obvious defects or issues with the suction pads.
- Monitor Load Weight: It’s imperative to ensure the sheet is within the correct Working Load Limits for the equipment.
- Checks Before Lift: The pads of the machine must be applicable to the material being lifted, guaranteeing stability and an established hold.
- Lift The Sheet: Raise the sheet slowly and establish that the vacuum is engaged and appropriately lifting the material. Continue until the sheet is completely moved to its next zone and not left unattended whilst suspended.
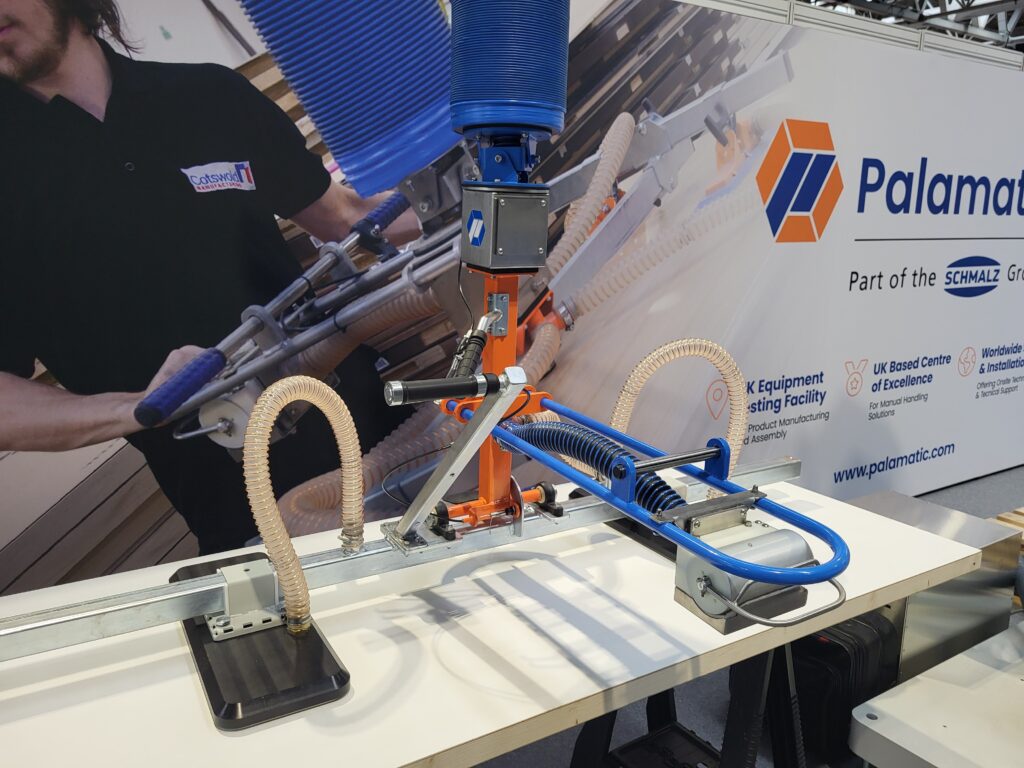
Contact Palamatic for Sheet Material Lifting Equipment
Vacuum lifters are invaluable at transforming material handling processes for various sectors, enhancing safety, productivity and streamlining operations. At Palamatic, we have over 35 years of experience supplying material lifting equipment worldwide, which is CE and UKCA marked for your peace of mind. Complemented with our gantry crane systems, our vacuum lifters deliver cutting-edge results which are also available in bespoke solutions.
If you’re looking for innovative solutions for sheet handling, get in touch with our expert team at Palamatic today.