Material handling involves numerous operational risks that can lead to workplace injuries and inefficiencies if not adequately managed. From repetitive strain injuries to accidents involving material handling equipment, the potential for harm is significant. Here at Palamatic, our 35-plus years of experience in providing material handling solutions informs all our practices; emphasising cutting-edge technology and innovative practices to mitigate risks.
Effective risk management strategies that organisations can adopt to ensure safety and efficiency in their material handling operations include:
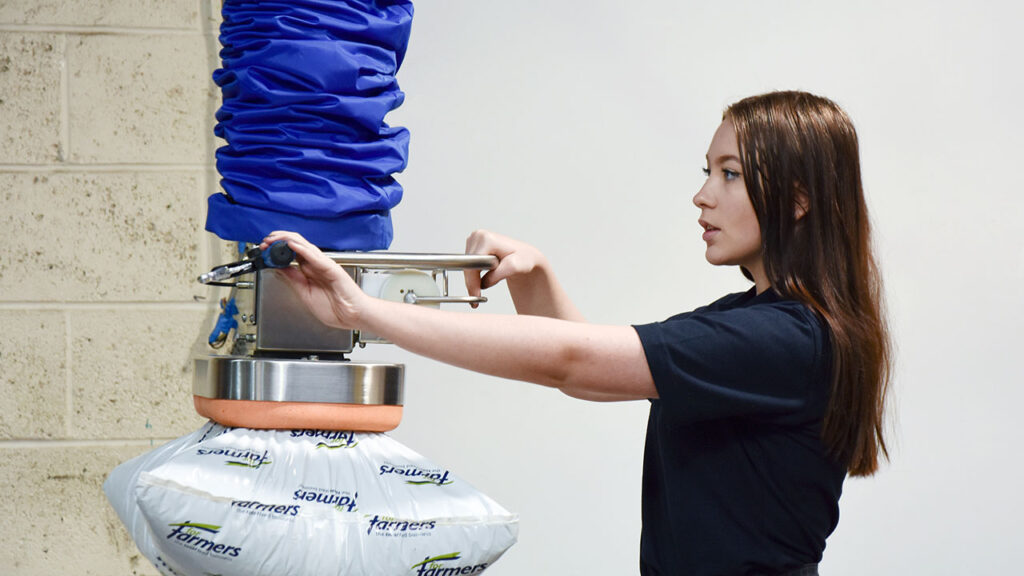
Implementing Ergonomic Solutions
Ergonomics plays a crucial role in minimising operational hazards. Equipment that is designed to match the capabilities and limitations of human performance not only reduces the risk of injury but also enhances productivity. Palamatic’s Industrial Vacuum Lifting Equipment is a prime example of ergonomic design, capable of handling up to 350kg with ease. These lifters assist operators with the repetitive lifting of sacks, panels, boxes, and more, which helps speed up the material handling process while protecting operators from the risk of accidents.
Utilising Hygienic and Safe Equipment Designs
In industries where contamination can be a significant risk—such as biotech, life sciences, and food processing—using hygienically designed equipment is essential. Palamatic offers Hygienic Stainless Steel Vacuum Lifters that are specifically manufactured for clean areas. These lifters are made from FDA-compliant materials and include special filtration systems and hand-demountable parts for simple cleaning and maintenance, ensuring the safe handling of delicate and contaminable materials.
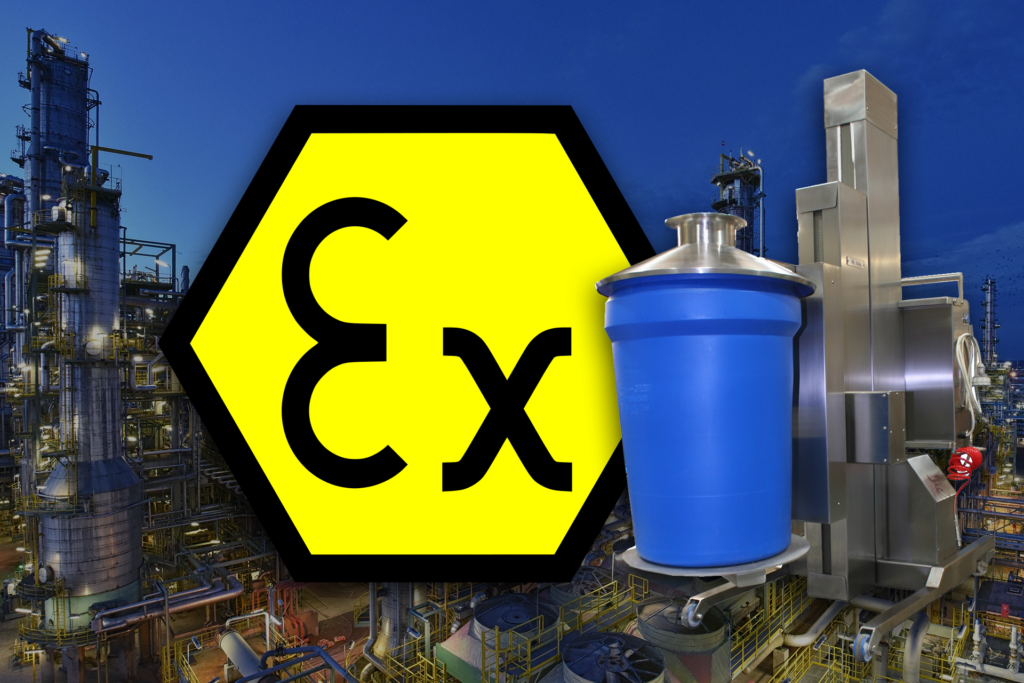
Adhering to Compliance and Safety Standards
Ensuring that all equipment complies with relevant safety standards, such as ATEX for explosive atmospheres and GMP for good manufacturing practices, is vital. Compliance not only helps in preventing workplace accidents but also ensures that the equipment can be used safely in specified environments. Palamatic’s equipment is compliant with such standards, offering solutions that are both safe and effective for specific industry needs.
Incorporating Advanced Dust Control Systems
In environments where dust exposure can lead to health risks or cross-contamination, employing advanced dust control systems is a critical strategy. Palamatic’s Dust-Free Sack Opening Systems are designed to protect operators from potential dust exposure and eliminate the risks of cross-contamination. These systems are particularly useful in handling products ranging from raw food ingredients to highly toxic chemicals.
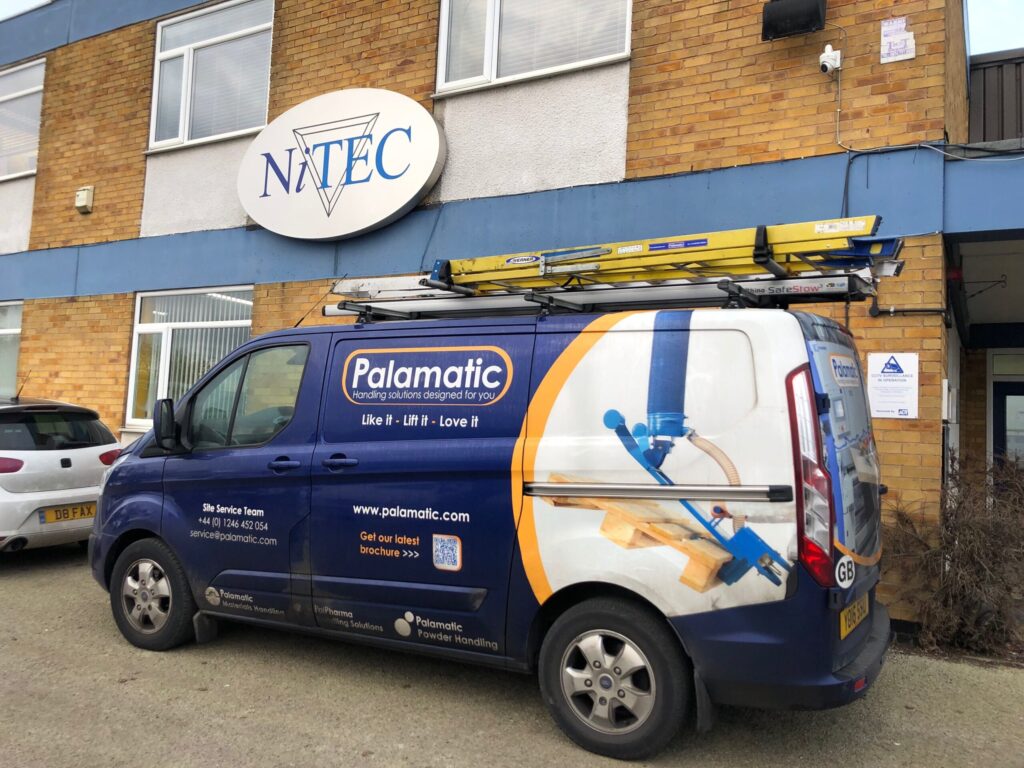
Regular Maintenance and Support Services
Regular maintenance is crucial to ensure that material handling equipment operates at peak efficiency and safety. Palamatic’s ongoing support, maintenance, after-sales services, and the availability of spare parts post-manufacture and installation ensure that their equipment remains fully operational and compliant with safety regulations like LOLER.
Customisation for Specific Operational Needs
Each operational environment has unique challenges and risks. Custom-designed material handling solutions can significantly reduce these risks by addressing specific needs. Palamatic’s ability to design and manufacture bespoke material handling equipment ensures that all operational hazards are considered and mitigated, providing tailored solutions that focus on efficiency, safety, and ergonomics.
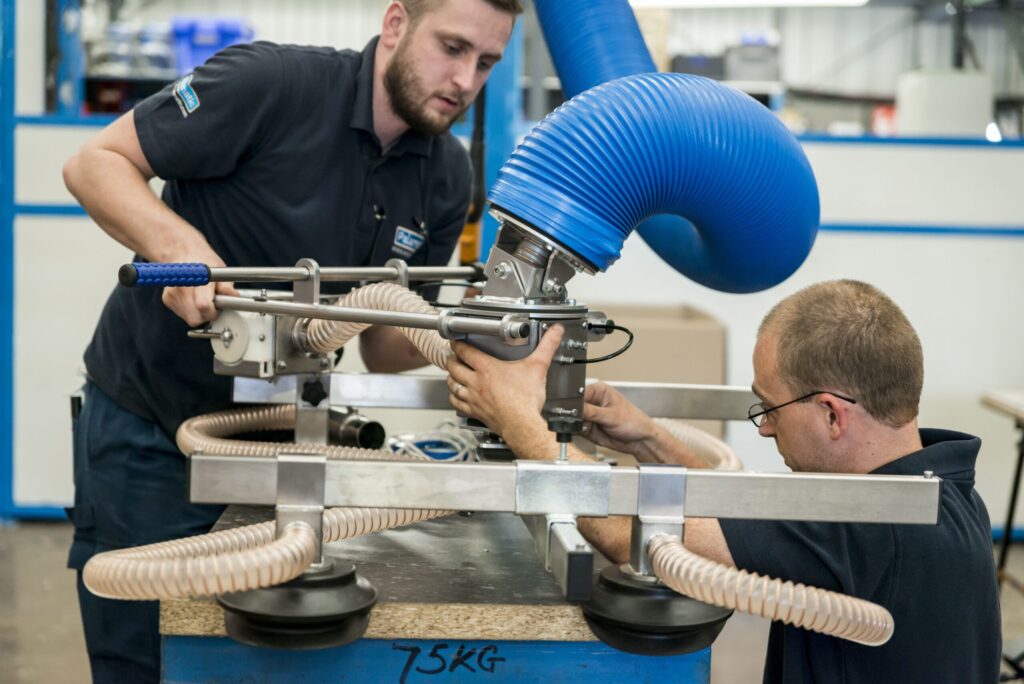
Training and Empowering Employees
Finally, educating and training employees on the correct usage of material handling equipment is indispensable. Comprehensive training not only minimises the risk of operational hazards but also empowers employees to manage risks more effectively themselves. Palamatic’s commitment to providing training, and holding competency certificates for LOLER, IPAF, PASMA, and more, underscores the importance of a knowledgeable workforce in risk management.
Trust Palamatic for Material Handling Solutions
By adopting these strategies, organisations can significantly reduce the risks associated with material handling and ensure a safer, more efficient operational environment. Palamatic exemplifies how integrating innovative design, compliance, and employee empowerment into material handling processes can lead to superior risk management and operational success.
For further information, or to enquire about our material handling solutions, contact our experts today.