Manual material handling can pose significant risks to employees and business operations through improper technique, poor safety protocols, and repetitive strain. By failing to understand the risks and undertaking effective procedures to mitigate hazards, the integrity of a company is compromised. Risk assessments ensure legal documentation is routinely carried out, offering invaluable data in helping identify and eliminate risks in the workplace.
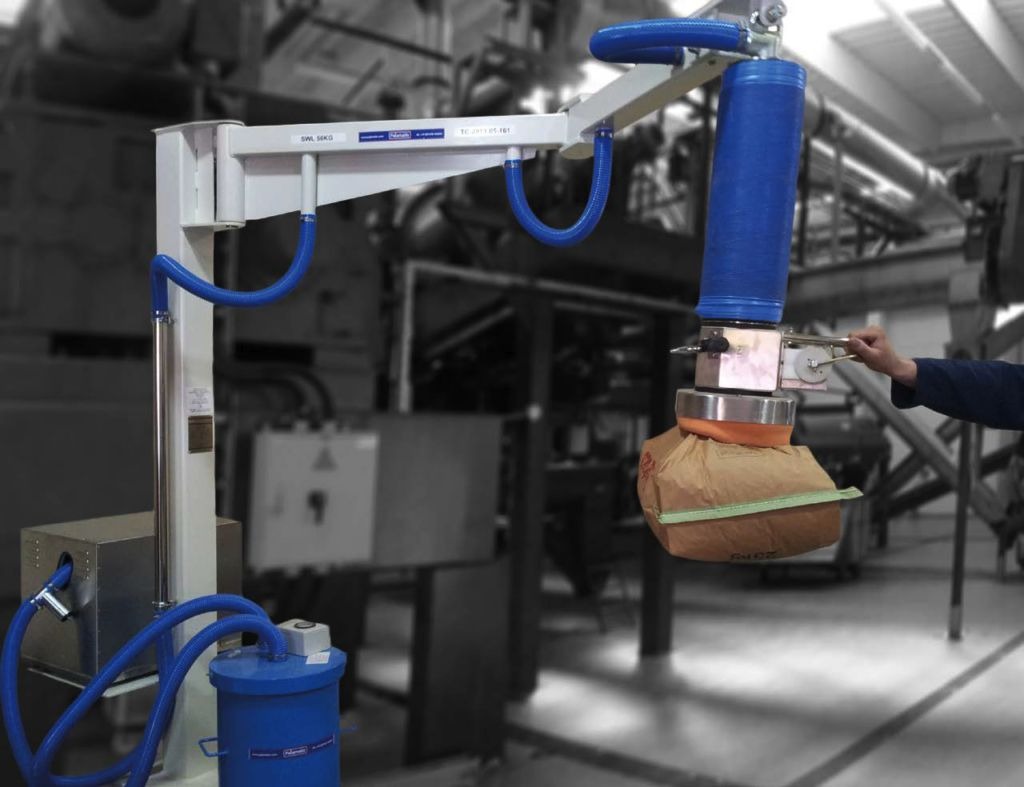
What Does Material Handling Involve?
Material handling can typically focus on two primary categories, manual and automated. Understanding each segment is imperative in order to carry out a thorough risk assessment. Both involve the movement of products and materials from one location to another throughout the manufacturing and distribution workflow.
Manual Handling
Utilising the legs, hands and body to transport differing loads, typically over extended periods of time. Range of motion includes:
- Lifting
- Lowering
- Pushing
- Pulling
- Carrying
Automated Handling
Material lifting equipment utilises automated power systems in order to facilitate processes and reduce strain on the body. Powered by a single operator, common types of equipment include:
- Automated Guided Vehicles (AGVs)
- Robotic Arms
- Conveyors
- Vacuum Lifters
- Cranes and Lifts
Employer Responsibility
1.7 million people suffered from work-related illness in 2023/24, according to the Health and Safety Executive (HSE). Despite the integration of material handling equipment, some form of manual handling will occur. It is the employer’s responsibility to provide efficient training, inspections and promote a safe and healthy workplace.
Responsibilities include:
- Routine training on correct manual handling techniques
- Employees must have suitable PPE
- Employees must be trained to identify hazards
- Sufficient training in equipment
- Regularly maintain equipment with certification
- Encourage open communication and assistance
The Manual Handling Operations Regulations 1992 was put into effect in order to mitigate unsafe practices at work. If employers are found disregarding health and safety within the workplace, they can be subject to large fines and a tarnished reputation.
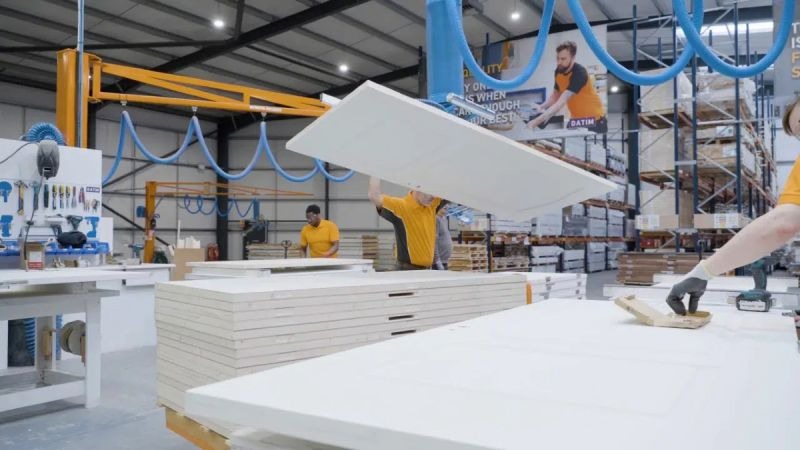
How to Conduct Risk Assessments for Material Handling
A risk assessment should be carried out at least once a year, with more frequency depending on the type of environment. When new equipment or procedures are adopted, an assessment must be completed upon implementation. In the workplace, a dedicated Environment, Health, and Safety (EHS) officer will be responsible for integrating policies, identifying hazards and ensuring employees are following health and safety procedures.
A manual handling assessment chart (MAC) is available as a tool to facilitate risk identification of manual handling, with care to ensure each report is tailored specifically to business operations.
Risk assessment checks
- Identify potential risks through observation, past incidents, manufacturer specifications, and employee concerns.
- Consider the severity level of each risk by calculating the consequence by the likelihood, determining a hierarchy risk rating scale.
- Recognise individuals who are at risk and how they might be harmed.
- How can the risk be controlled and what safety parameters are in place?
- Are employees sufficiently trained in the equipment and/or role?
- Record keeping of all findings with fully dated assessments.
- Revise assessments when a change in the workplace occurs, such as new procedures, equipment, or staff changes.
The consequences of a risk can be determined by five main categories, these are as follows:
- No injury or an insignificant injury – Does not require first aid
- Minor injury – First aid required.
- Moderate injury – Requires further treatment, non-permanent illness/injury.
- Major injury – Requires treatment from a hospital and/or permanent illness/injury.
- Catastrophic – A fatality.
Separate risk assessments are required for each piece of equipment due to them typically posing their own set of unique challenges. If a piece of equipment is considered complex, it may undergo further checks to understand how to combat risks that can arise.
Why are Risk Assessments Important to the Workplace
Not only are risk assessments required by law in the UK, but they also provide irrefutable benefits for the business, employees, and visitors to company facilities.
Preventing incidents in the workplace: the primary objective of risk assessments are to eliminate the risk of injury and maintain safe environments. This protects people, and can even save lives, by instilling long-term safety awareness across all procedures.
Shift workplace culture: businesses should ensure all employees across each area, regardless of hierarchy, are aware of health and safety practices. This is important in order to ingrain best practices throughout all operations, with senior roles leading as an example.
Gain depth of business operations: identifying risks and monitoring severity levels ensures that a greater understanding of the full-scale business workflow is understood, offering valuable data and insights into areas of concern.
Documentation: risk assessments will always require sufficient documentation, which is beneficial when needing to conduct audits, showcase compliance, and obtain safety accreditation.
Eliminate lost revenue: with risk assessments, a budget can be clearly defined and delegated across different sectors, while reducing lost revenue from employees taking sick days due to workplace injury.
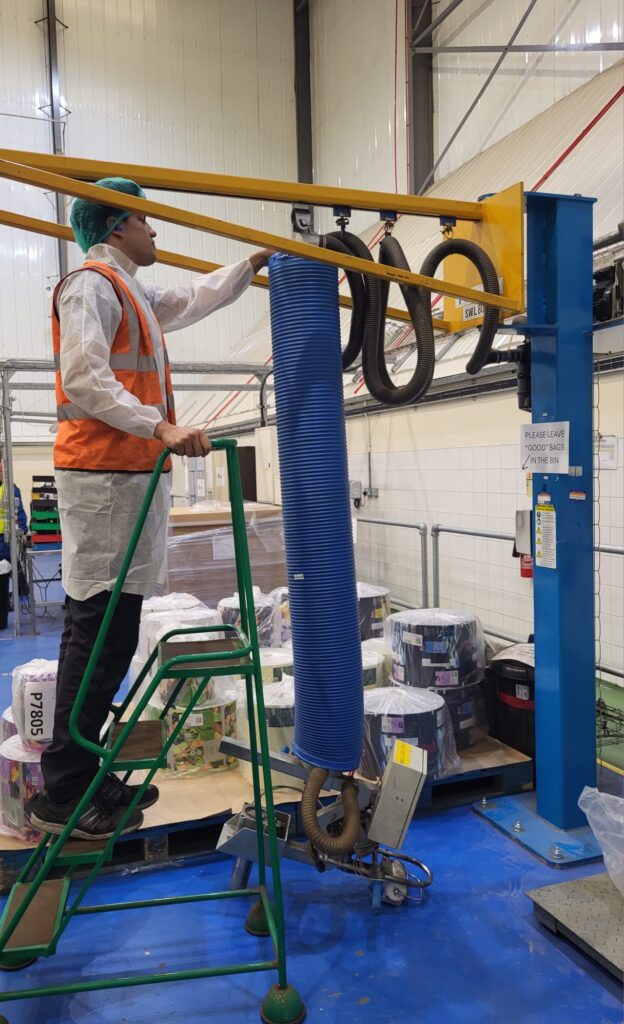
Prioritise Health and Safety with Palamatic
Since 1985, our mission has been to design, manufacture, and install material handling equipment that is safe and meets regulatory standards, regardless of industry. We strive to ensure your business has professional equipment that is compliant, effective and provides excellent results.
Our leading equipment encompasses vacuum lifters, gantry crane systems and dust-free sack opening solutions for ergonomic lifting and optimised processes. At Palamatic we go beyond, offering bespoke design for your requirements and additional ongoing maintenance support.
For further guidance on our safety-compliant material handling equipment, get in touch with a member of Palamatic today.