Demanding industries often require rapid results, which is why at Palamatic, we understand that material handling equipment needs to be fit for the job every time. It’s crucial not to overlook the significance of regular maintenance of material handling equipment. Maintaining high-quality standards for business operations is not only cost-effective but also increases safety and productivity within the workplace.
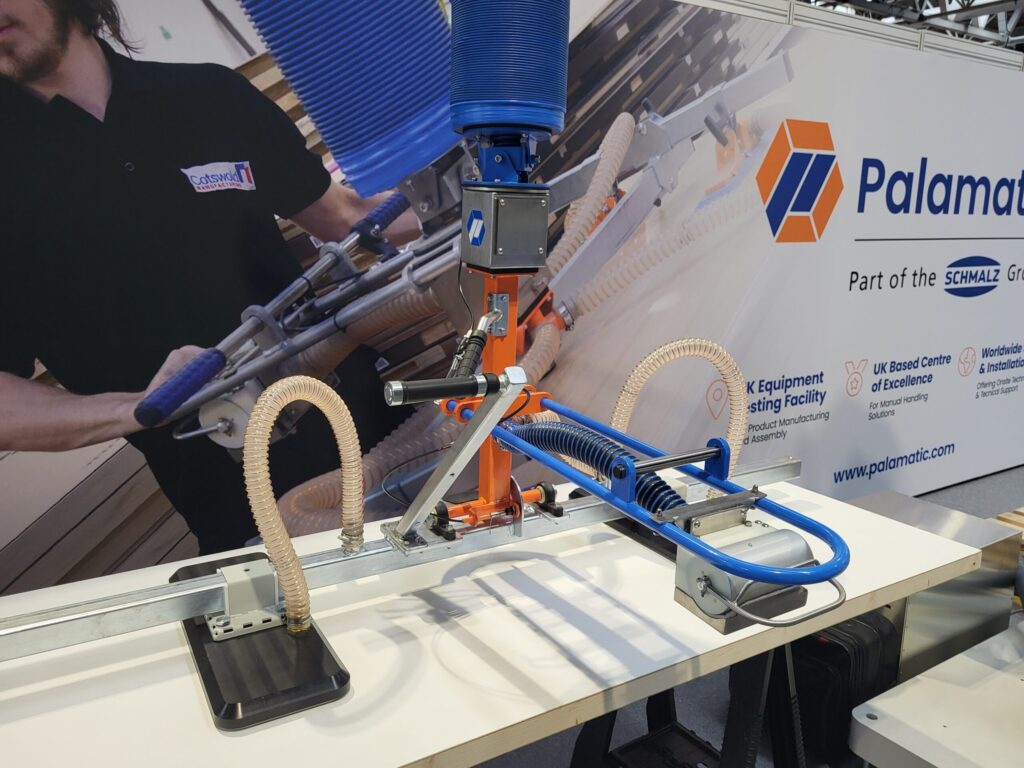
Why is Preventative Maintenance for Material Handling Equipment Important?
Operating an effective workplace environment with optimised performance means taking measures towards the industrial equipment workers use daily. Automated, busy and heavy-duty industries should monitor equipment to ensure responsible workplace efficiency. Preventative maintenance means taking precautions before equipment failure or workplace injury occurs.
Implement Safe Workplace Conditions
Since 1985, Palamatic has been campaigning for workplace safety. Palamatic provides professional material handling equipment to various sectors across the globe and has been instrumental in understanding how important safety in the workplace is. Investing in maintenance to ensure your equipment is always in excellent condition is imperative and invaluable to the business; the Health and Safety Executive (HSE) states that 35.2 million working days are lost due to work-related illness and injury in 2022/23.
Reduced Operating Expenses
Investing in material handling equipment maintenance allows for long-term reduced operating expenses. Mitigating the risk of workplace injury creates fewer sick days and reduces the risk of loss of productivity. This also results in equipment not requiring to be replaced as frequently, which increases expenses significantly.
Increase Equipment Lifespan
Material handling equipment does not have to be used until the point of failure or the cause of a workplace accident. Regular maintenance allows increased longevity for your equipment, resulting in fewer equipment replacements and wasted resources.
Optimise Workplace Operation
When dealing with busy work environments, especially with heavy-duty equipment, making sure the workplace is consistently optimised for efficient workflow is a necessity. Reduce breaks in the line of operation from equipment failure and streamline your business with maintenance servicing.

How Often Should You Carry Out Inspections?
Daily Inspection
Senior staff and employees need to carry out inspections of equipment before use. Taking time for quick visual checks and that systems operate as they should allows for the work day to be utilised effectively and safely.
Monthly Inspection
Checking material handling equipment monthly is imperative for those closer inspections. Monthly inspections are the time to observe filters, lubrication and other essential elements of your equipment.
Annual Inspection
Yearly inspections allow for a more in-depth overlook of material handling equipment and should be performed by a professional maintenance team.
LOLER 1998
Material handling equipment must undergo examination by LOLER 1998. This legislation reduces workplace risk and is required every 6 to 12 months or after each time equipment is installed. Palamatic offers annual inspections and invaluable service contracts for your convenience.
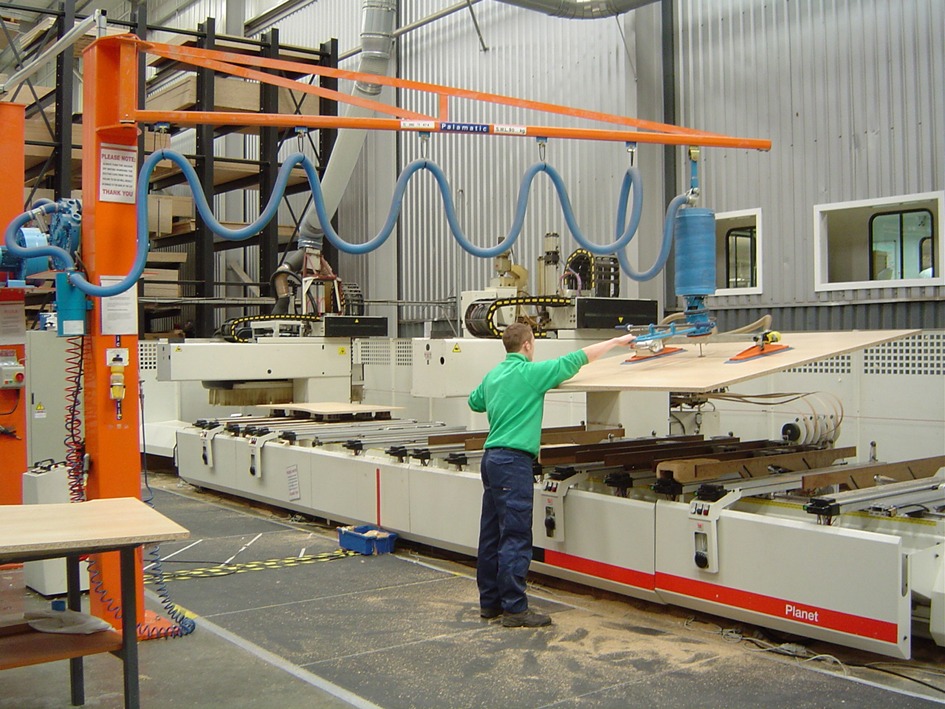
How to Carry Out Visual Inspections for Material Handling Equipment
Electrical Faults and Contamination
It is necessary to check for exposed wiring that may be contaminated by oil, grease, water, or dirt.
Correct Operating Systems
All aspects of the operating systems should be functional, with any relevant audio cues working as they should. Systems should be kept up-to-date in line with manufacturers’ recommendations.
Equipment is Operating Sufficiently
Routinely perform audits such as de-vacuum and drop tests before each use of equipment to ensure they are working correctly.
Check Equipment Attachments
Attachments such as suction feet/hooks etc. should be checked for any wear and tear that could impact the performance of the equipment or pose a risk to safety.
Equipment Damage
Inspecting the equipment for damage is imperative, such as checking the suction pads remain in good standard for operation.
Sufficient Lubrication
Checking that there is sufficient lubrication where required allows the equipment to run as efficiently as possible and increases lifespan.
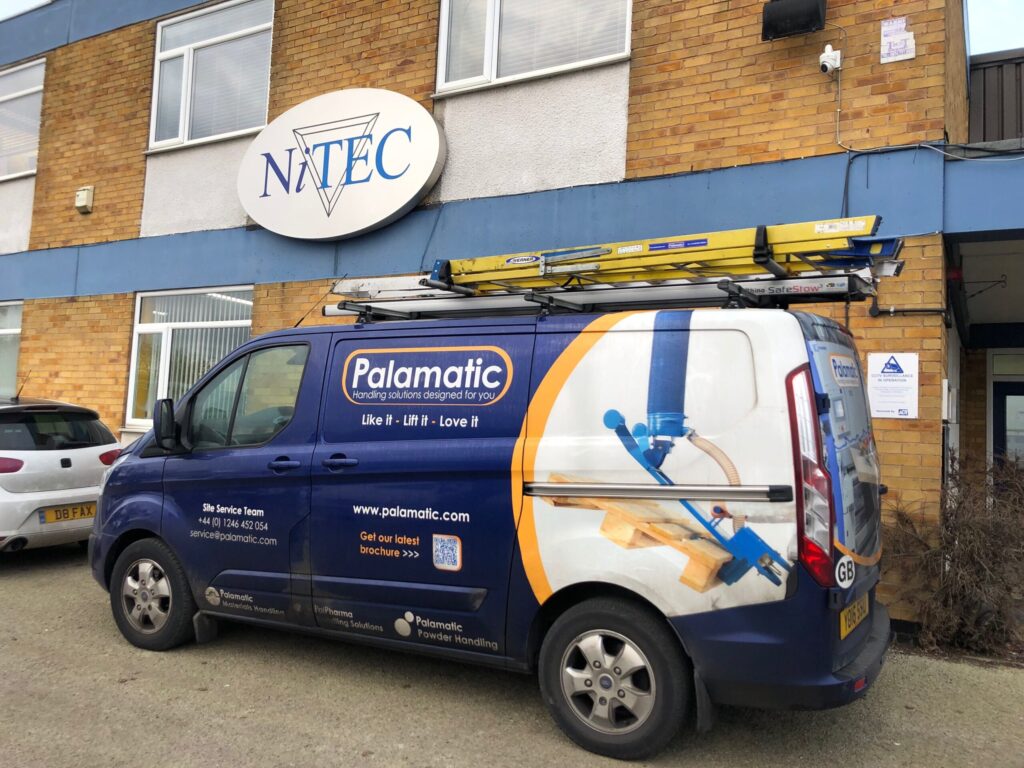
Trust Palamatic for Material Handling Preventative Measures
Taking steps towards preventative maintenance for your material handling equipment ensures that the business can run efficiently and increase productivity. Not only does it comply with health and safety standards, but it showcases professionalism for business operations and employee welfare. Embrace preventative measures by performing regular audits, and keeping employees up to date with safety protocols.
For further support, or to discuss annual servicing inspections, get in touch with Palamatic’s team of professional experts.